Is your JSA collecting dust?
- Deborah Grow
- Jan 28, 2018
- 2 min read
Updated: Jan 2, 2019
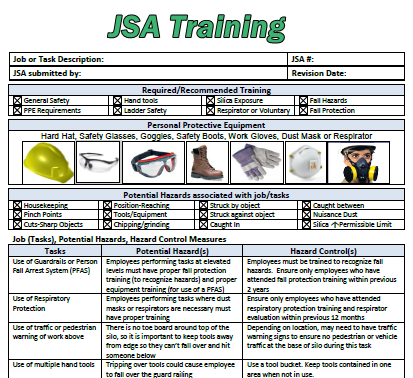
If your JSA is collecting dust in a book on a shelf somewhere, you are missing out on the single most effective tool you have in your safety toolbox!!!
The JSA tells you the:
– Task
– Hazard
– Hazard Control
If the JSA is well written, identifies all the hazards and all your controls are effective, and you trained all employees on the JSA (Safe way to do the job), then there should not be any accident. If there is a close call or near miss, be sure to review the JSA and make necessary changes and retrain employees.
Train all employees in the JSA for the task you plan to do
(takes all of 5 minutes to review it before beginning)
– Daily-Review the hazards and how to work safe
– Review the JSA for the task just before starting the job
– It reminds employees of the hazards and how to work safely
Perform routine job safety hazard analyses (JSA, JHA, or JSHA)
· Hazard analysis techniques can be quite complex. While this is necessary in some cases, frequently a basic, step-by-step review of the operation is sufficient. One of the most commonly used techniques is the Job Hazard Analysis (JHA). Jobs that were initially designed with safety in mind may now include hazards or improper operations. When done for every job, this analysis periodically puts processes back on the safety track.
· Other, more sophisticated techniques are called for when there are complex risks involved. These techniques include: WHAT-IF Checklist, Hazard and Operability Study, Failure Mode and Effect Analysis, and Fault Tree Analysis.
Change Analysis
Anytime something new is brought into the workplace, whether it be a piece of equipment, different materials, a new process, or an entirely new building, new hazards may unintentionally be introduced. Before considering a change for a worksite, it should be analyzed thoroughly beforehand. Change analysis helps in heading off a problem before it develops.
You may find change analysis useful when:
Building or leasing a new facility.
Installing new equipment.
Using new materials.
Starting up new processes.
Staffing changes occur.
Author: Deborah Grow, Safety Compliance Specialist
Private Safety Consultant, Sales-Marketing Director Damon Fall Protection and Coordinator EHS Network ~ Kansas.
Follow me on:
Comments