Create a Strong Safety Culture
- Deborah Grow
- Sep 22, 2017
- 2 min read
Updated: Jan 2, 2019
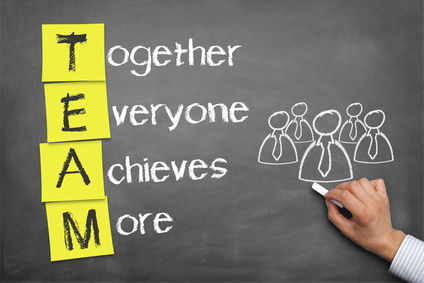
According to OSHA, “Safety cultures consist of shared beliefs, practices, and attitudes that exist at an establishment. Culture is the atmosphere created by those beliefs, attitudes, etc., which shape our behavior.” By definition, safety culture is difficult to measure. How do you measure values, attitudes and beliefs?
Tap into your employee's knowledge and unleash the potential within every employee! If you seriously involve your employees in safety, your safety and health program will really take a leap in the direction you want it to go!
A safety culture is built through the establishment of a fundamentally sound safety program
Management commitment (All managers and supervisors must be held accountable for safety performance BEFORE you can hold employees accountable. Many of the things that it takes to improve your overall safety performance and reduce accidents, takes money and management is in total control of the money, the employees have little control over what safety equipment is purchased or how much time is devoted to training or performing the necessary safety activities it will take to reduce accidents)
Policy statement (Everyone is responsible for safety and everyone is expected to participate in safety activities. Safety is not optional)
Program goals (Specific~Measurable~Achievable~Realistic~Time Targeted) Remember that What gets measured gets done. What gets' recognized gets done well
Employee training (First focus training on hazard recognition and reporting. Employees learn better by visual and practice. Teach Back & Games most effective in retaining information)
Employee recognition: Participation + Recognition=Motivation to Excel. People will go above and beyond expectations to be recognized for their efforts. (The only way to change the safety culture is to get the employees motivated and involved in safety. The best way to motivate employees is with positive recognition for stepping up for safety) The Safety Recognition must be linked to achieving the Annual Goals and Objectives. If you do what you've always done, you will get what you've always gotten. Don't link the recognition to injuries, people may fail to report those minor injuries which will end up being major injuries because you didn't know about them and did nothing to fix the problems. Link the recognition to what you are doing (safety activities like inspections, observations, toolbox safety talks, stepping up and taking initiative without being told to do something), not to what isn't happening.
§ People don’t do what you “expect”, they do what you “inspect”. Inspections should be done in EVERY area at least EVERY week-Identifying and correcting hazards will reduce or eliminate potential for an employee to have an injury. If you are not finding hazards, you aren't looking very hard!
Hazard analysis / correction: People don’t do what you EXPECT, they do what you INSPECT. Inspections should be done in EVERY area at least EVERY week-Identifying and correcting hazards will reduce or eliminate potential for an employee to have an injury. If you are not finding hazards, you aren't looking very hard!
Leadership is the ability of a single individual, through their actions to motivate others to a higher level of achievement!
Recognition motivates people to do better and to exceed your expectations. Enthusiasm is contagious!
Author: Deborah Grow, Safety Compliance Specialist
Private Safety Consultant, Sales-Marketing Director Damon Fall Protection and Coordinator EHS Network ~ Kansas.
Follow me on:
Comentarios